If a 8K (mirror) stainless steel sheet is scratched by accident, how can I rescue it? If the scratch is not very serious, during mirror polishing, you can slow down the feed roller speed and lower the grinding head to make the scratched area as smooth as possible.
It is generally understood that there are several situations where mirror stainless steel scratches appear:
The first is that the sheet is scratched before processing, it is just not obvious, this requires judging the severity of the scratch. If the scratched area and scratched depth have exceeded the customer's acceptance of the final product effect, then the sheet that meets the requirements should be replaced. That is, the inspection of the processing operator is very important.
The second is that the sheet has been mirror-finished, but it was accidentally scratched during the filming process. There are many kinds of such scratches, such as: point scratches, linear scratches, and large-area scratches. Point-like scratches, regardless of the depth, can be repaired by argon arc welding, then polished with a grinder, and then processed by mirror polishing equipment for two or more times. This problem can basically be solved.
How to deal with scratches on stainless steel mirror sheet?
If it is repaired on the bright surface, the polishing method can be used, and the polishing wheel of different meshes can be repeatedly polished. In general, sandblasting is used for matte surface repair, which requires special equipment. If the wire drawing panel has been done in the early stage, special equipment is also required. No matter which method is used, the surface must be passivated at the end. It is judged as a slight scratch. If it is a mirror surface, you can polish the stainless steel surface with polishing wax. If it is a wire drawing, you can use a wire drawing machine to wire the stainless steel surface.
Then there are linear scratches, which are what we call scratches. It is relatively difficult to deal with scratches. Shallow scratches can be solved by the above method (slow down the speed of the feed roller and lower the grinding head). Deep scratches are not easy to handle. Lishun stainless steel recommends that you try to avoid scratches when processing and cutting the mirror panel material.
In addition, when talking about large-scale scratches and scratches, there are two types of scratches, and the treatment methods are the same as above.
If it is the second type of scratch, it is more difficult. Because this kind of secondary scratches should be avoided as much as possible. It is recommended that you reduce or avoid the possibility of scratching the mirror panel by the following methods: sticking a protective film on the surface of the board, packaging the board with a wooden frame, padding the board or plastic board on the board, packing the whole with waterproof paper, and expressing "protection" on the board or packaging surface Good surface, don’t scratch” and other words. If the finished mirror stainless steel plate has scratches, it can basically be done according to the method mentioned above. If it is a semi-finished equipment, and the surface is mirrored with scratches, you need to use a variety of polishing equipment; such as a hand-held polishing machine that can replace multiple polishing wheels to achieve a better repair effect.
The satin finish is achieved by brushing the stainless steel in one direction using a grit abrasive belt followed by a softening and buffing process which creates a less shiny but glossy look, compare with mirror polishing, it is a matte finish, not reflective.
4B finish, it is a mill finish, which is not available with us and not common seem in the market, but you probably know No.4 finish and #4 fnish, but this is a processed surface finish by abbrasives.
No.4 is a finish mostly accepted by the whole world stainless steel users, it is not a directonal brushed short hairline with surface protective film laminated over the processed surface, prevent it from scratches and possible damages during transition and fabrication.
Well, this is truely a nice question, PVD coating accutally is a material called titanium coated over the surface, this material will harden the surface and make the material more wear resistant.
Compred with electoplating, PVD coating is a good option as it is a extremely thin coating, only a few microns thick, and the coating layer is nearly impossible to get removed, except by physical method, Otherwise if will last as long as the stainless steel and won't wear off on its own.
2B finish is a type of cold rolled stainless steel, it is a mill finish, original surface finish comes out of re-rolling mills, where changes the hot rolled stainless steel into cold rolled stainles steel.
It can be used for structual and functional use, non decorative purpose.
Further surface processings like brushing, grinding or polishing, color coating, sand blasting, etc., all can be done over the it, which the processings will max using of the stainless steel application scope.
The protective film on the stainless steel plate is an effective measure to prevent scratches and damages over the surface. Therefore, we don't recommend removing it before processing, such as cutting, bending, welding, polishing, and other processes.
We have found some people who didn't remove the file after installation, especially some outdoor projects, it will make the later cleaning work very difficult, why is that? just because Because the protective film is a chemical product, it is prone to deterioration and oxidation if exposed to high temperature and light for a long time. It should be used as soon as possible during the warranty period, and the warranty period is generally three months, a better-imported film like Novacel, Polifilm, the general warranty period is within six months to one year. When selecting and using the film, choose the appropriate film according to the use environment, product, object, and season.
What we should do to remove the protective film easily?
1. You can quickly tear off the film with boiling water, it will make the separation work easier.
2. Wipe with thinner or industrial alcohol do the first cleaning, then use water to clean and dry the sheet surface.
3. If you want to store the sheets for a long time, we suggest you choose imported brands.
For more, please feel free to contact us at info@goldecosteel.com
There is a surface processing called AFP in stainless steel industry, then what is AFP?
AFP is short for anti-fingerprint, it is thin coating by rolling or spraying the acrylic resin modified oil over the sheet surface then dryed under fixed high temperature.
It has great advantages:
- Prevent fingerprints and oil stains from sticking and erasing easily
- Smooth surface, comfortable hand feeling, not easy to get scratched
- Different optical properties, does not change the original texture, affects the original color.
Contact us at info@goldecosteel.com for more!
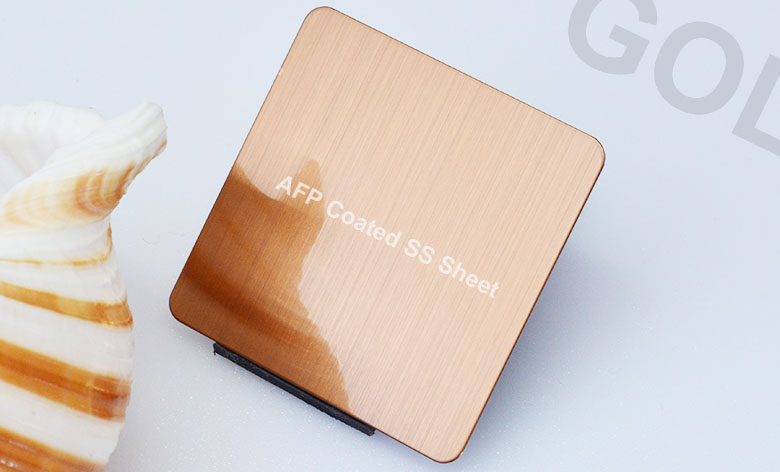